Helicopter Functional Surface Development TM
Advanced solutions to simplify your operations
Amaris-Performance-Nanotechnology™ | Helicopter
Advanced solutions to simplify your operations
We solve these important operational issues
1. TRANSPARENCIES: Scratched, swirled or hazed transparencies
2. TAIL SECTION: Degradation due to exhaust heat ans soot
3. PAINTWORK: Bug smearing & embedding
4. CLEANING: Frequent time consuming cleanups
5. DEGRADATION: Surface exposure to operational friction
SITUATION 1
Scratched, swirled or hazed transparencies
Due to the friction required to remove bug protein and stains, transparencies are bound to rapidly develop swirls and scratches which impair in flight visibility, even on new equipment.
The solution:
Transparency-Functional-NanotechnologyTM | TFNTM
Refinishing: Amaris' transparency process allows even severely swirled transparencies to be restored with high definition opticals. Our proprietary multi-stage process returns to your windshield and windows to a superior finish which greatly impacts pilots' comfort and safety.
Nanotechnology Layering: Amaris installs a functional-nanotechnology shield over polycarbonates and acrylic surfaces. TFNTM layering gives uncommon crystal clear visibility in the most adverse flight conditions. Our clients systematically report crystal clear visibility in the rain, even making drizzle a non issue. Bug smearing is very easy to wipe off as it does not stick to the Nanotech surfaces .
Call Us Before replacing your windshields or windows, it may not be necessary!

2010 BELL 429
Removal of damaged windshield hardened acrylic coating and installation of our TFCTM module

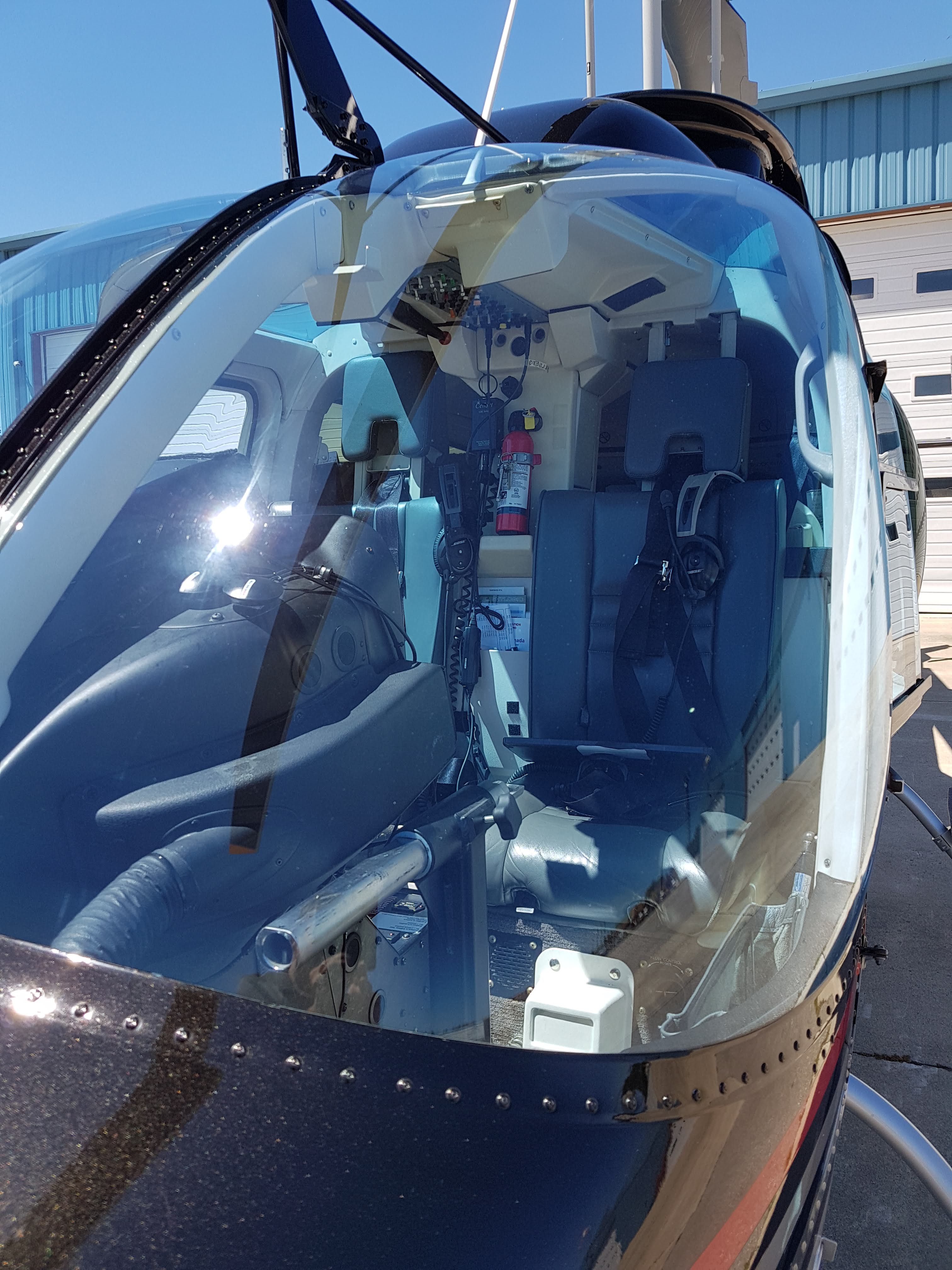
2007 BELL 206
Original windows - TFCTM package
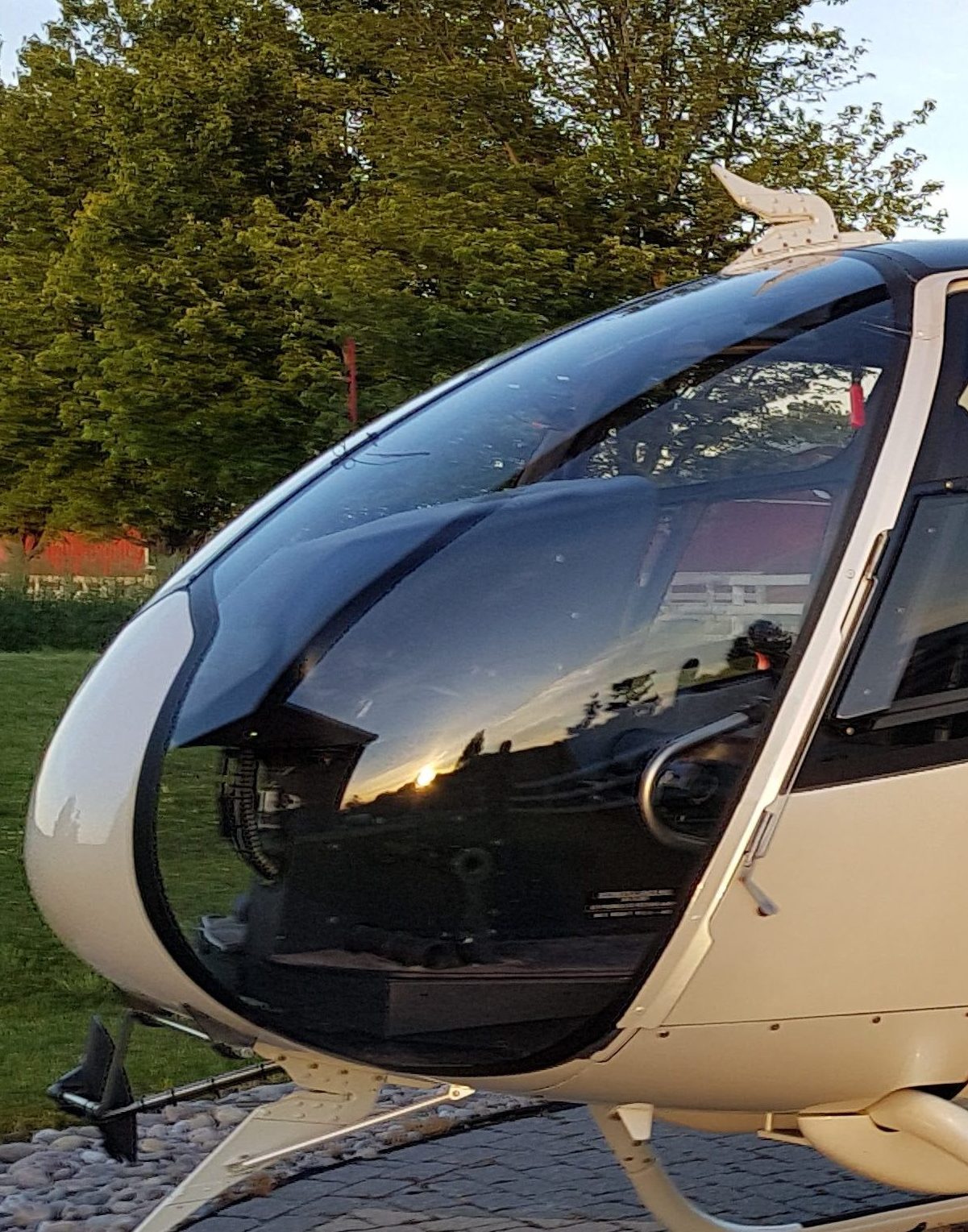
2006 EC 120
Original windows - TFCTM package
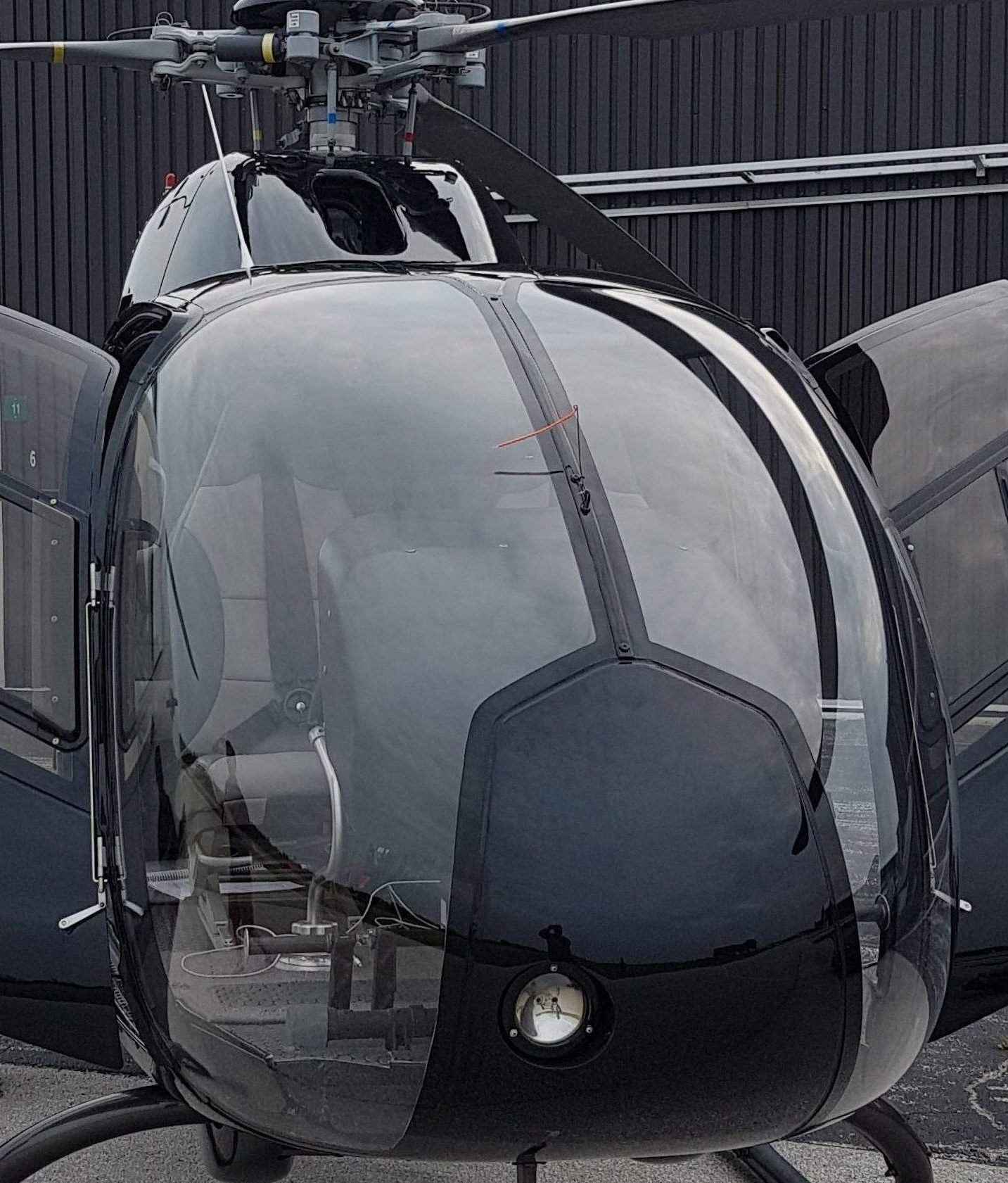
2004 Eurocopter EC 120
Original windows - TFCTM package
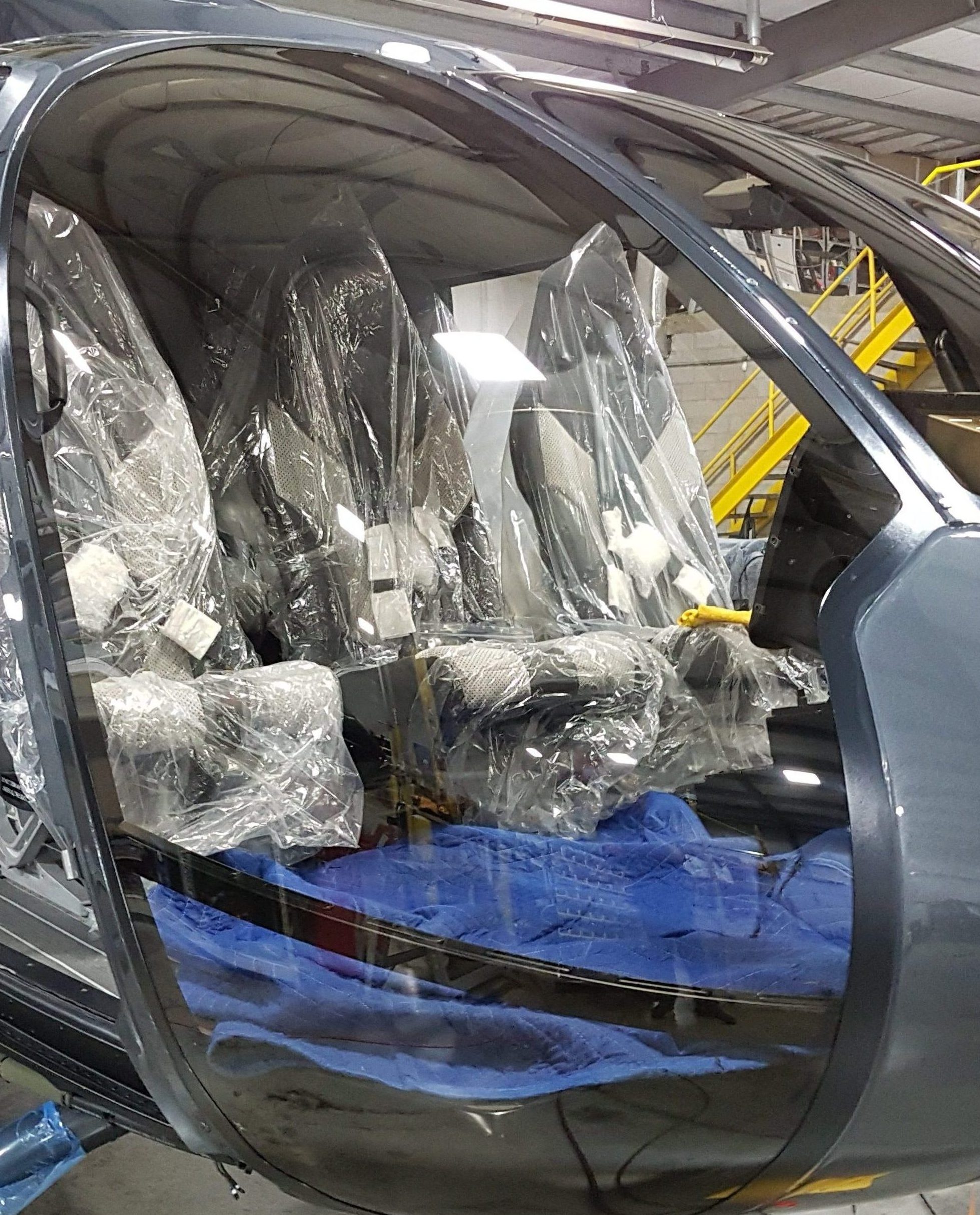
2008 Eurocopter EC 130
New windows jeweling + TFCTM package
SITUATION 2
Degradation due to Exhaust heat ans soot
Turbine helicopters notoriously propel massive exhaust heat mixed with soot combined with the velocity of prop wash cause severe stress on the surface tail section.
The solution: Aviation-Functional- Nanotechnology | AFNTM
Amaris' Functional Nanotechnology provides breakthrough benefits to helicopter operators. The amount of soot build up is greatly reduced thanks to the hyper sleekness of the Super-Surfaces and the physical characteristics ensure long lasting solutions even in demanding operational environement and flight schedule.
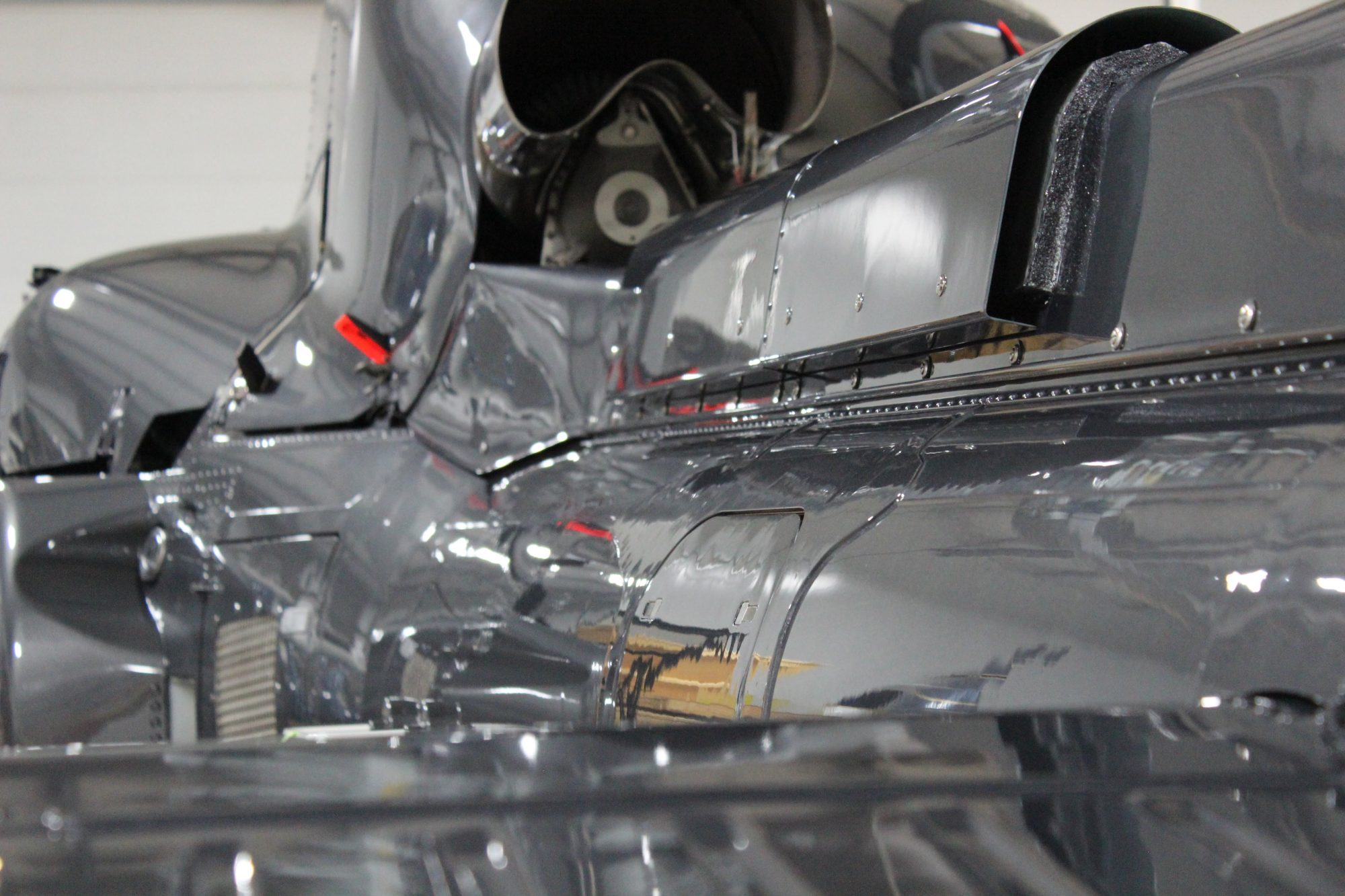
Protecting the new paintwork
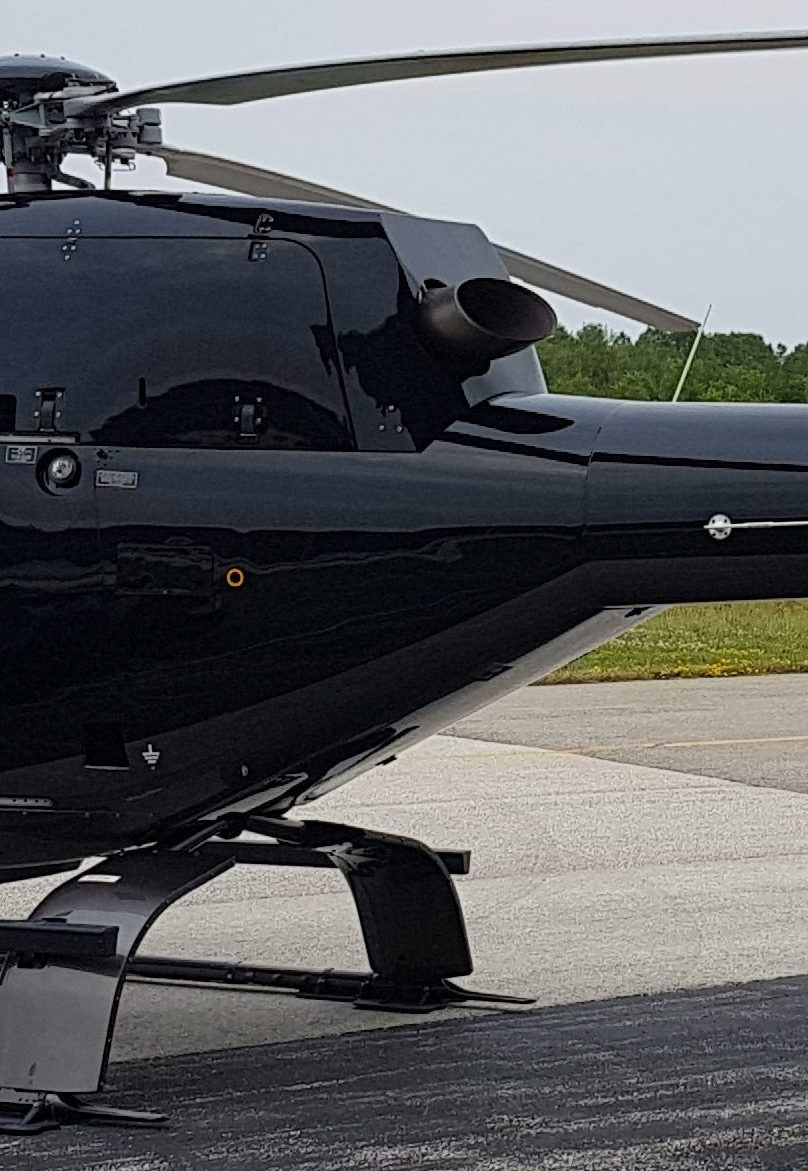
2004 EC 120
Cowling | tail section FCSTM
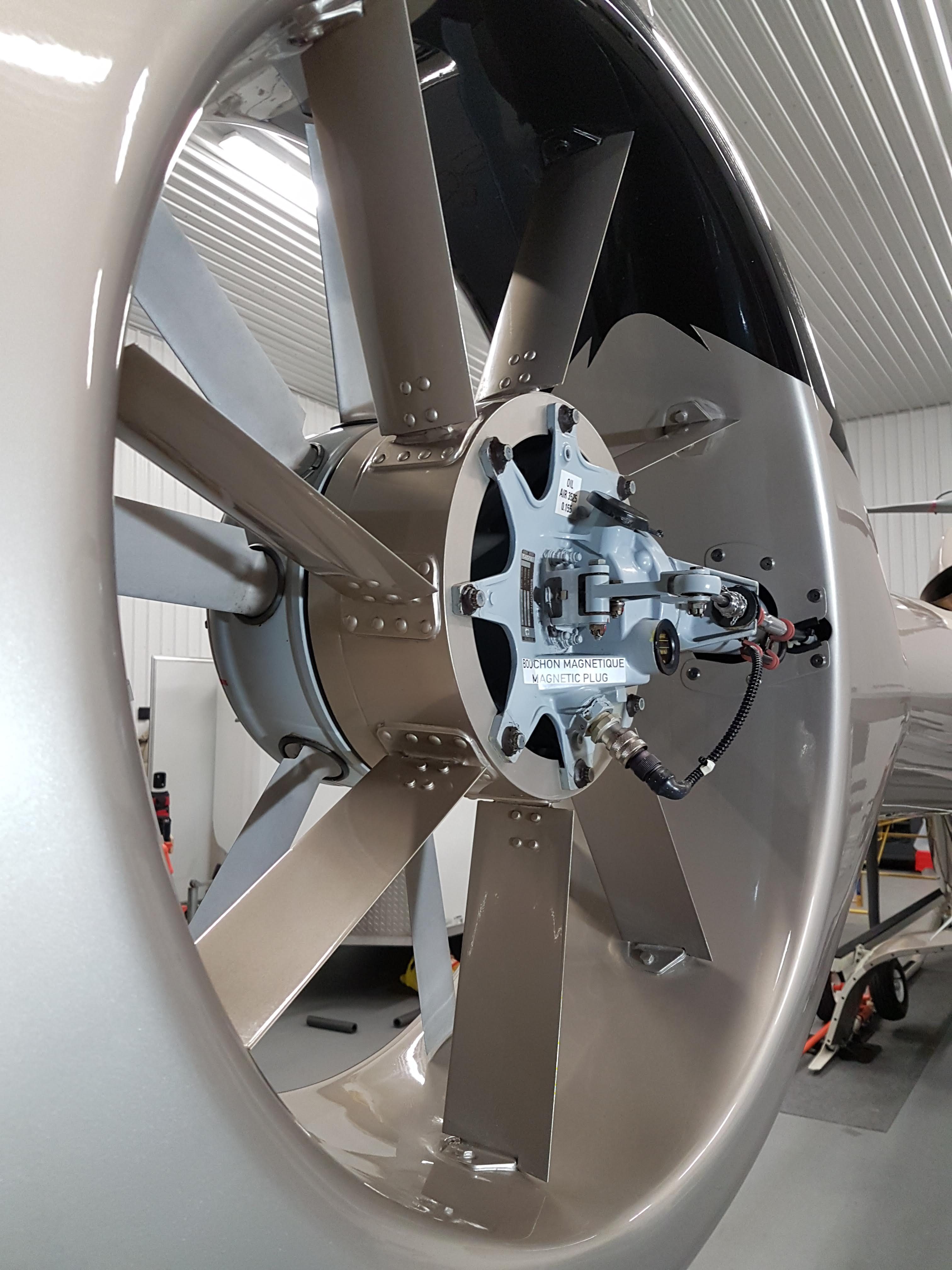
2006 EC 120
Fenestron easy to keep clean
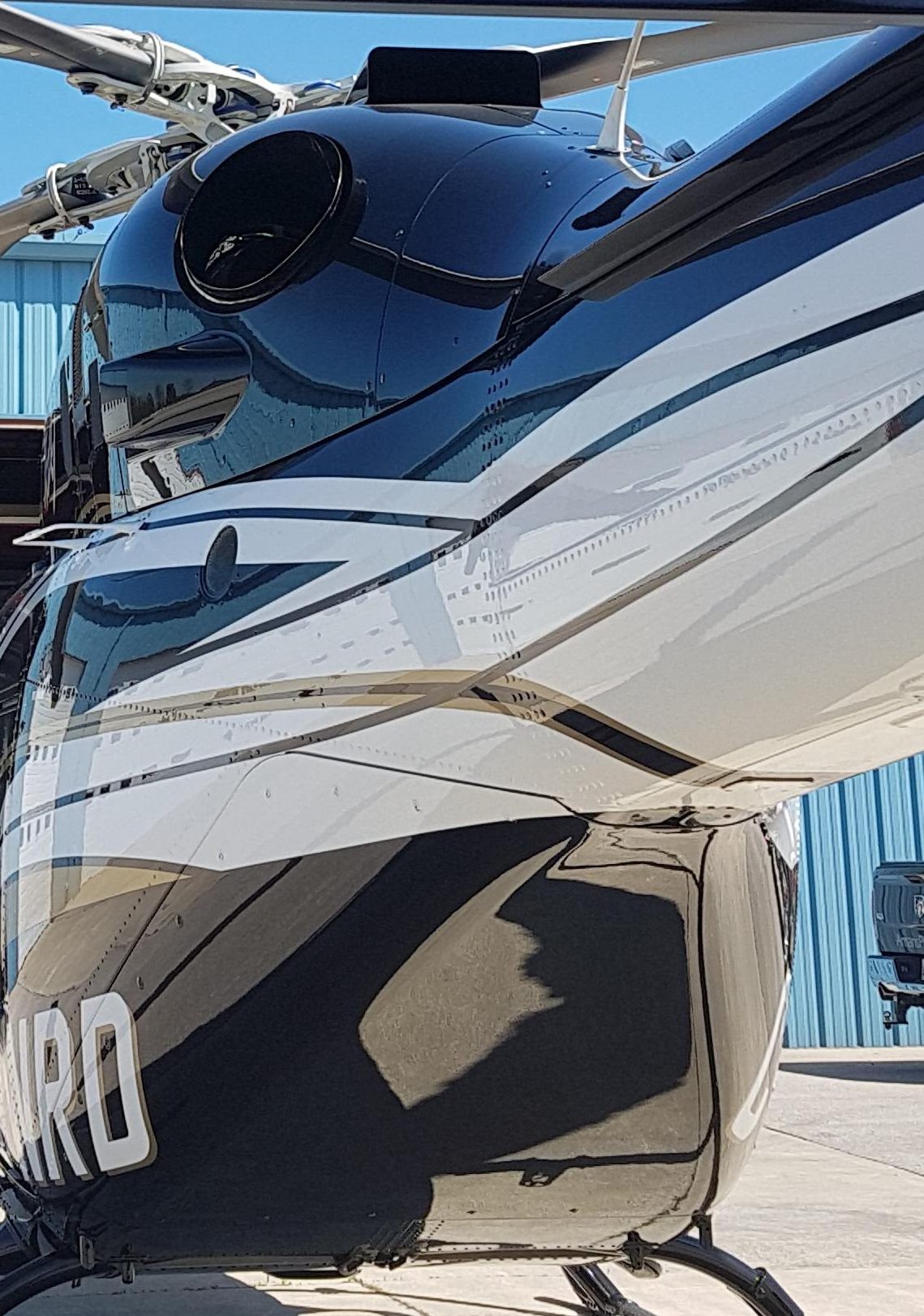
2010 BELL 429
Cowling | Tail section FCSTM
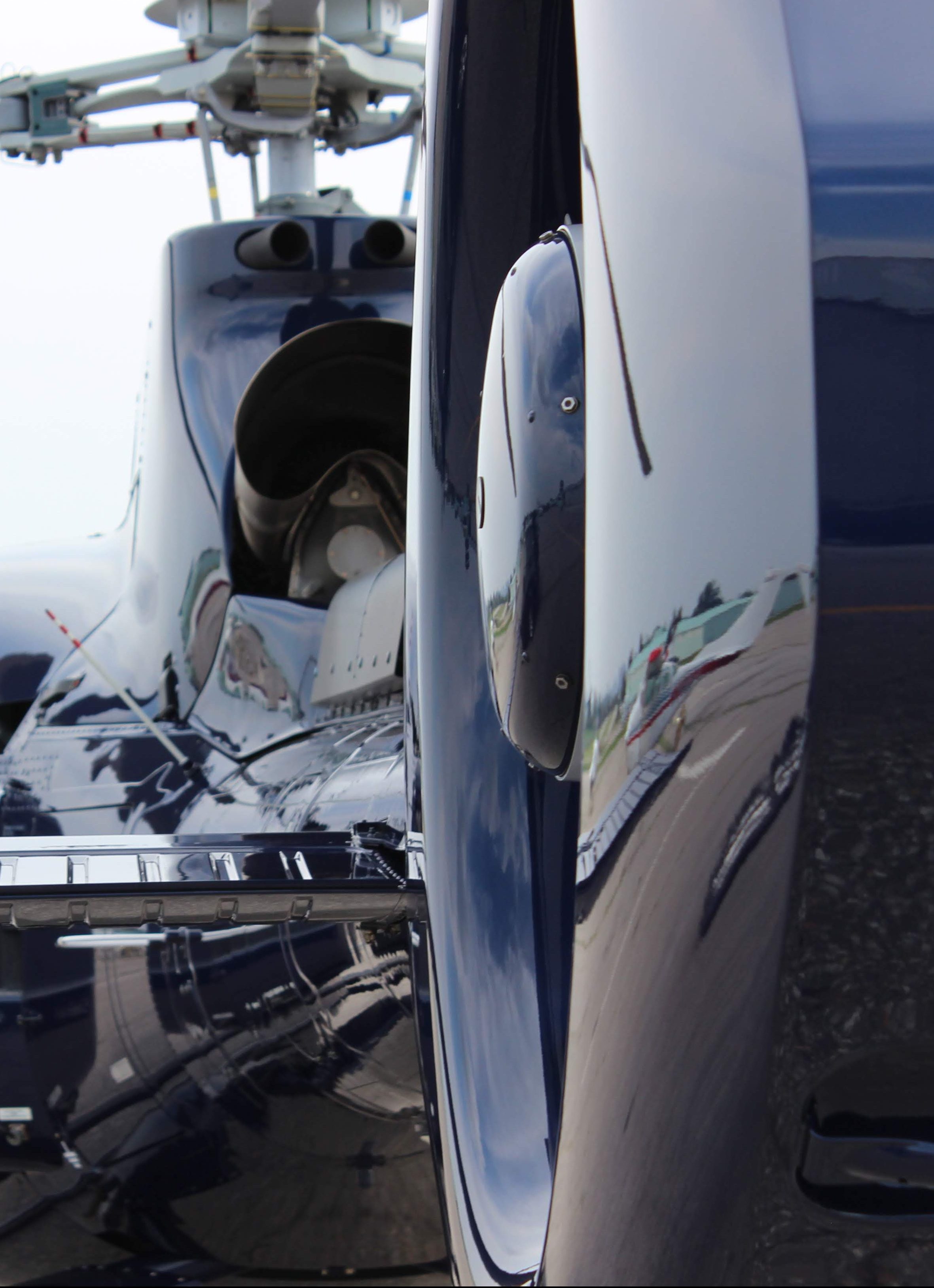
AIRBUS H130 T2
FCSTM Ultra Package
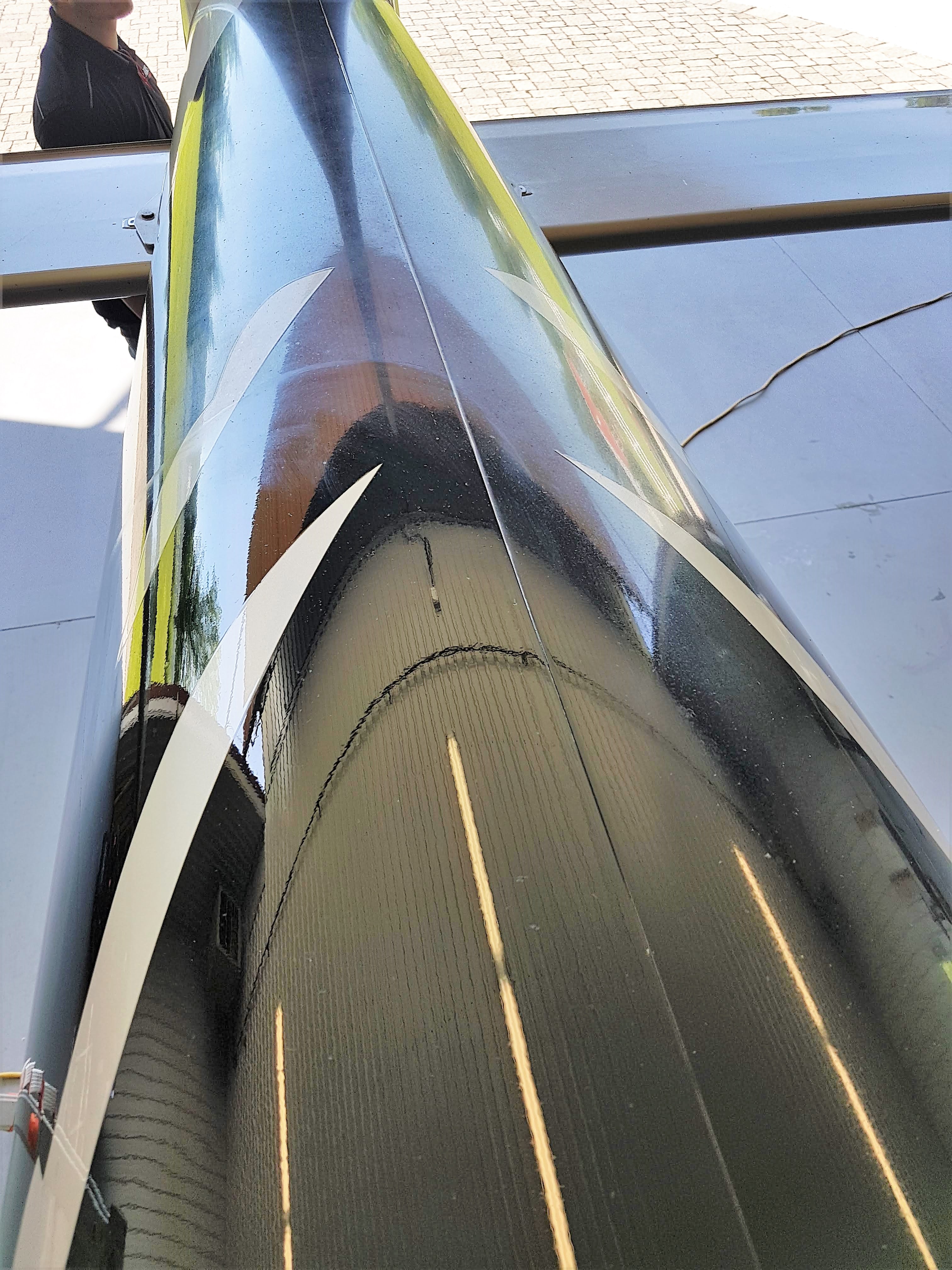
2006 EC 120
(Original Paint)
Severe clear coat heat damage
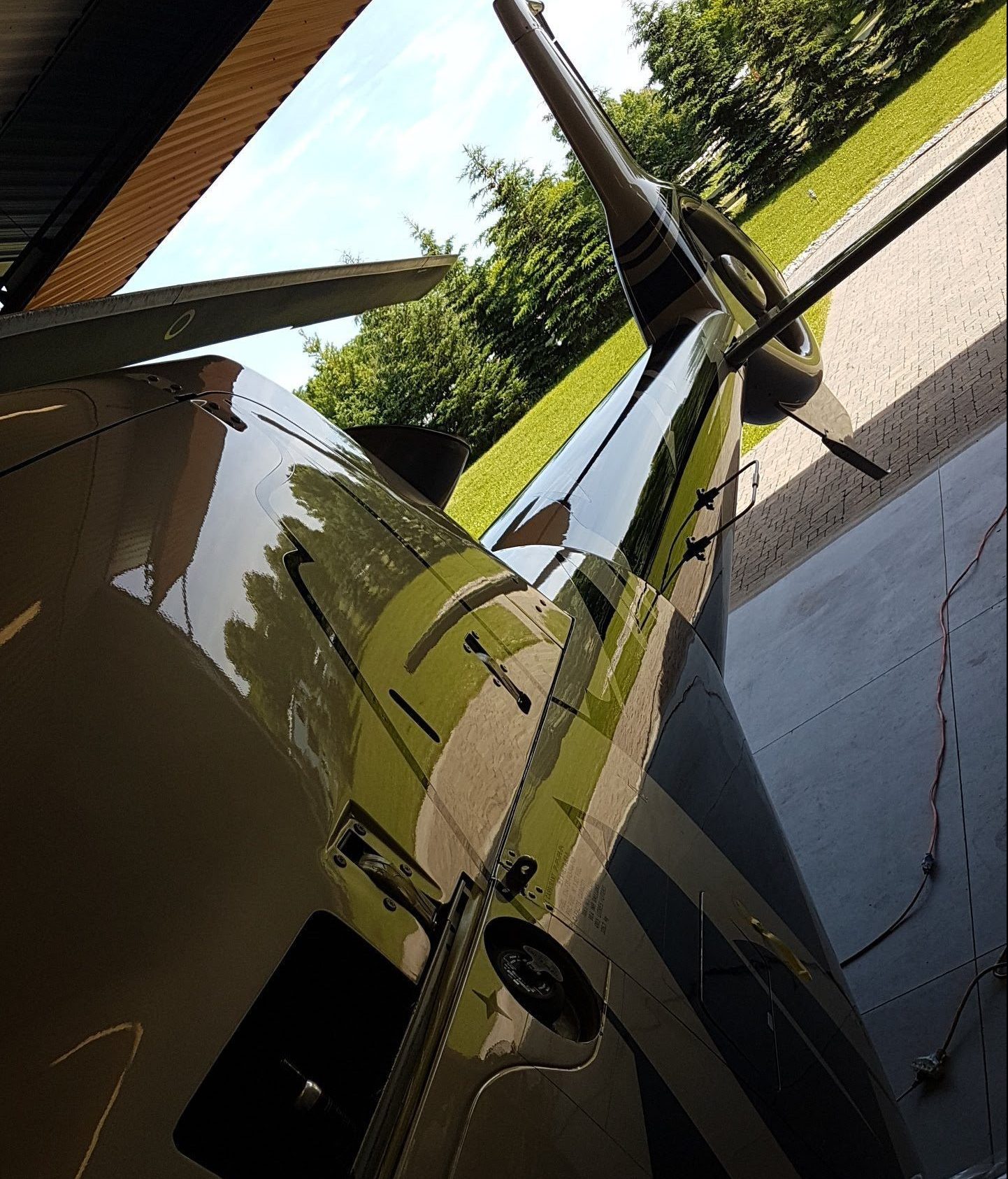
Return to high level finish | Amaris' FSCTM shields the tail section from future heat exposure
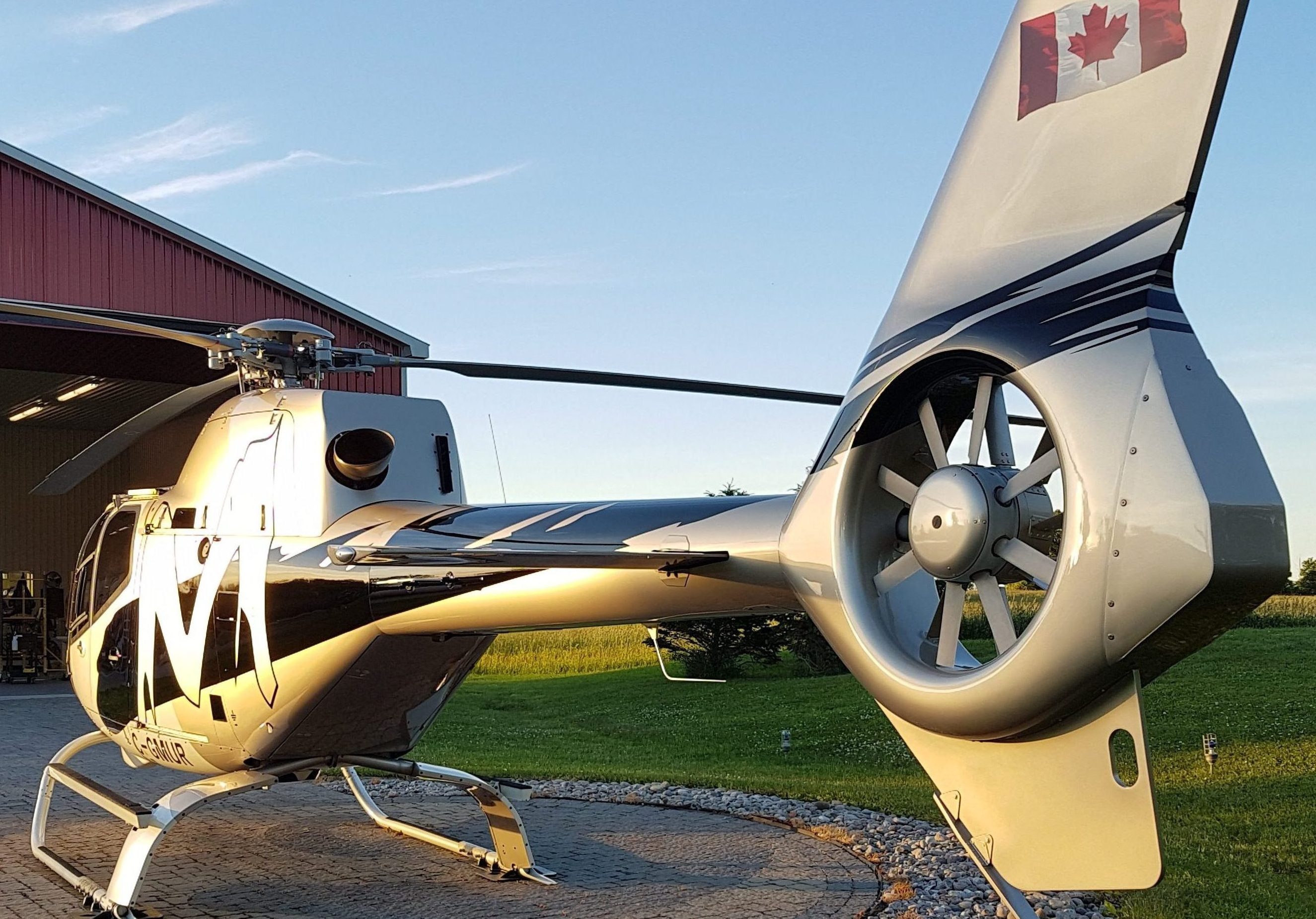
The inherent quality of the surfaces reflects in inspiring aesthetics....
SITUATION 3
Bug smearing and embedding
The impact of bugs has negative consequences that go beyond cleanup issues. Bug protein will actually embed itself into the paintwork. Buffing will only remove the excess layer of protein, however chemical contamination remains in the paintwork.
The solution: Aviation-Functional- Nanotechnology | AFNTM
Amaris renders your helicopter paintwork immune from bug protein contamination. Bugs wipe off easily thanks to the extreme sleekness of the nanotechnology. The physical resilience of our installation will also guard your paintwork from physical impact.
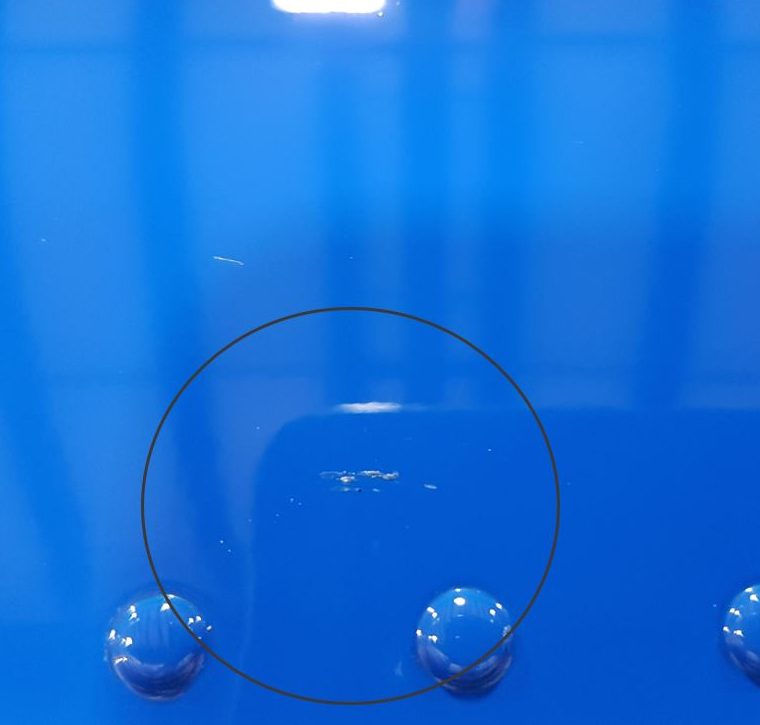
Embedded protein remains after buffing
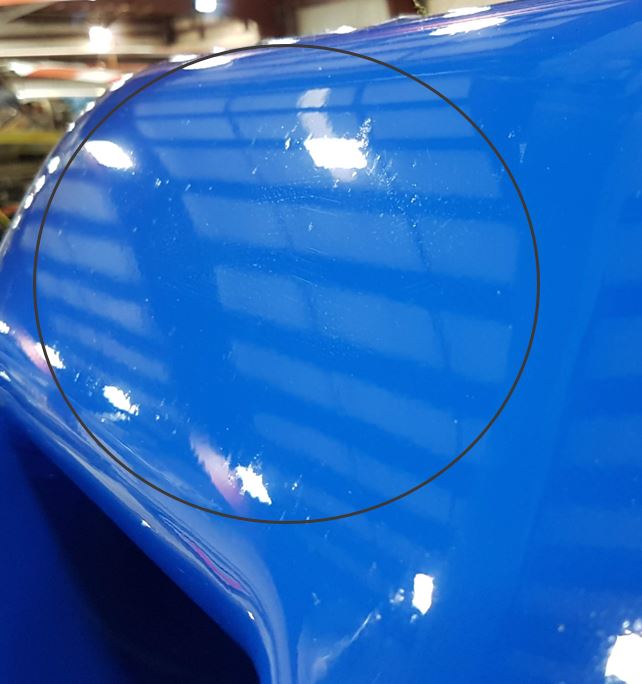
Bug impact damage on air intake
2017 Airbus H125
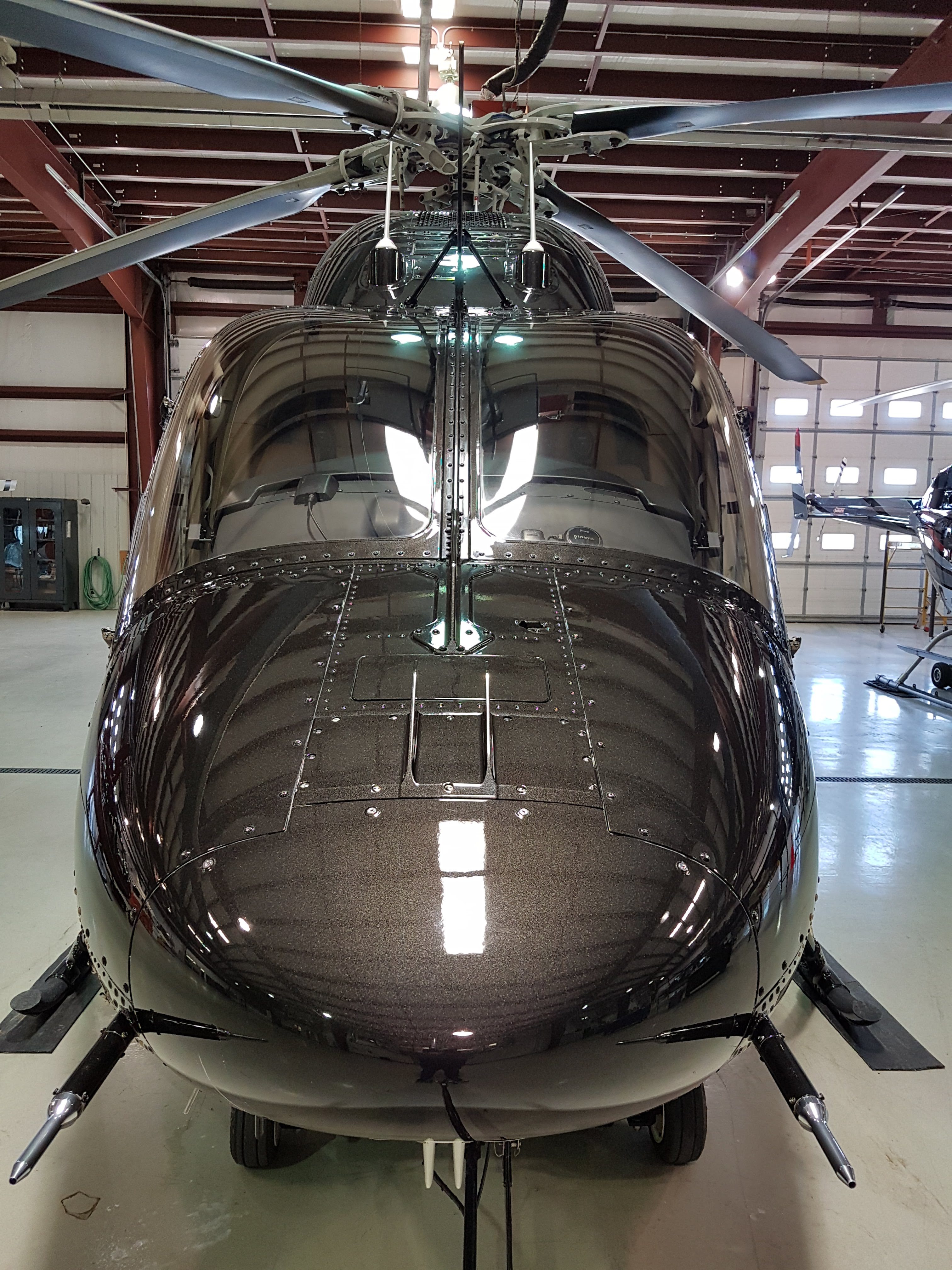
2010 BELL 429
Shielded for bug impact

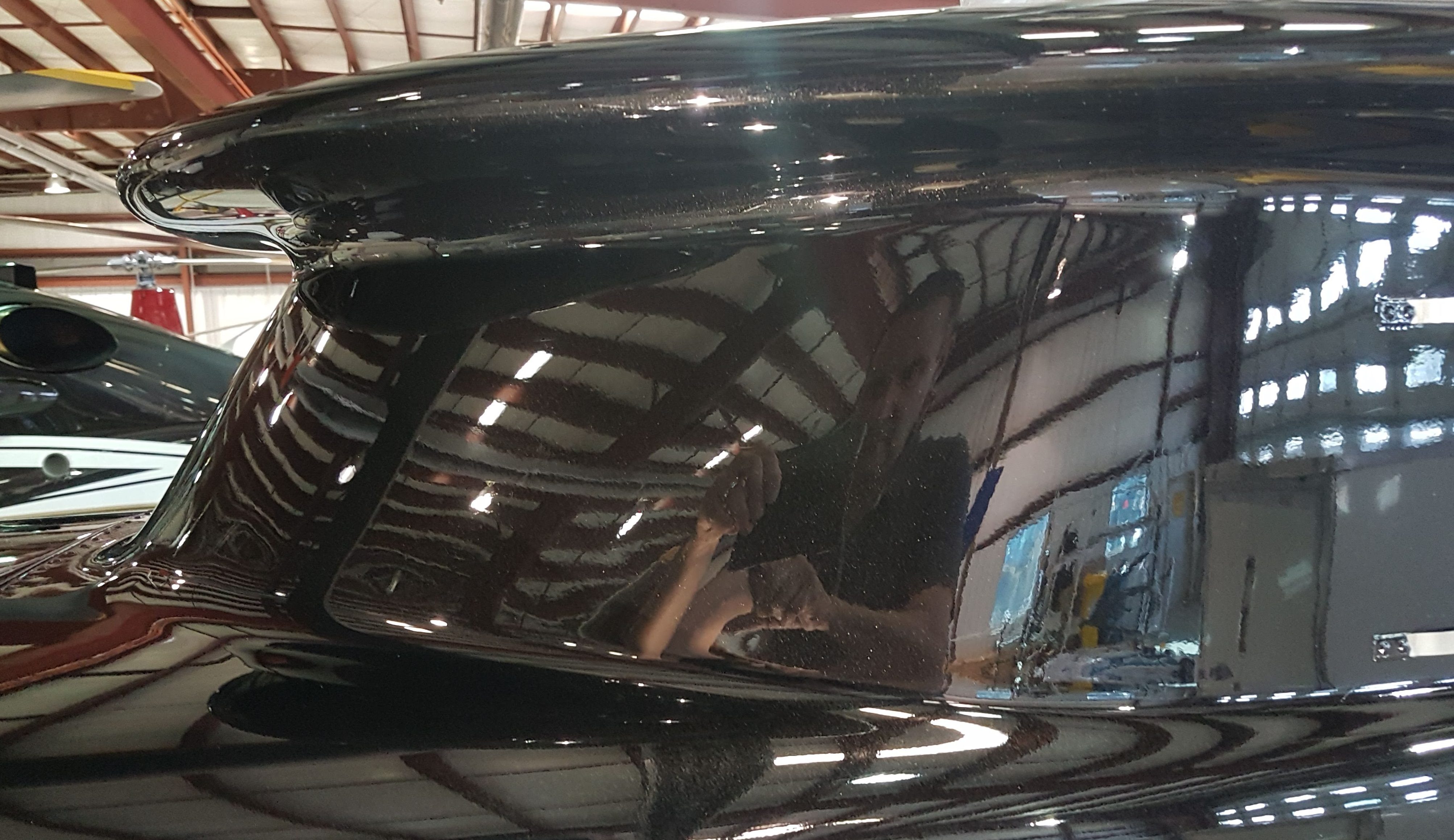
2007 BELL 206
FSDTM and FSCTM program results on this 11 year old helicopter
SITUATION 4
Frequent Time consuming cleanups
Turbine helicopter operators typically experience difficulty keeping the tail section clean due to lack of available downtime and the cost of ongoing cleaning.
The solution:AFNTM Super sleekness to the rescue
Functional in nature, Amaris AFN Nanotechnology offers enduring super sleekness which reduces soot accumulation on your turbine helicopter. It dramatically shortens the wash time. No more time consuming scrubbing, as contaminant lifting and rinsing procedures become the new normal. Any moisture is blown off in minutes with compressed air or leaf blowers in remote operations!
Enjoy our accelerate wash procedures to go from dirty to detailed over the entire aircraft in 1 hour!
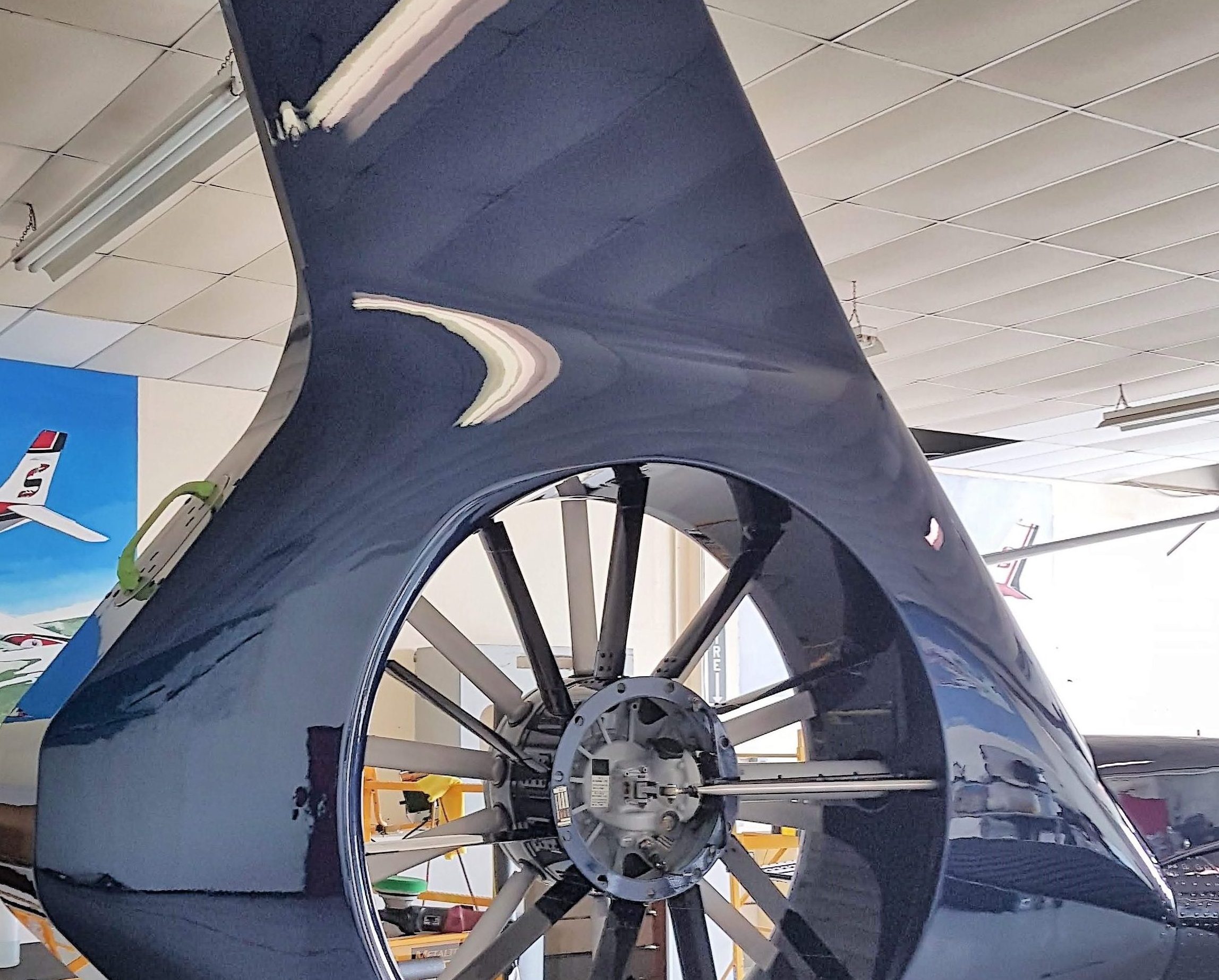
2015 Airbus H130 T2
2015 AIRBUS H130 T2
Complete wash with thorough detail finish can be completed in 90 min by one person
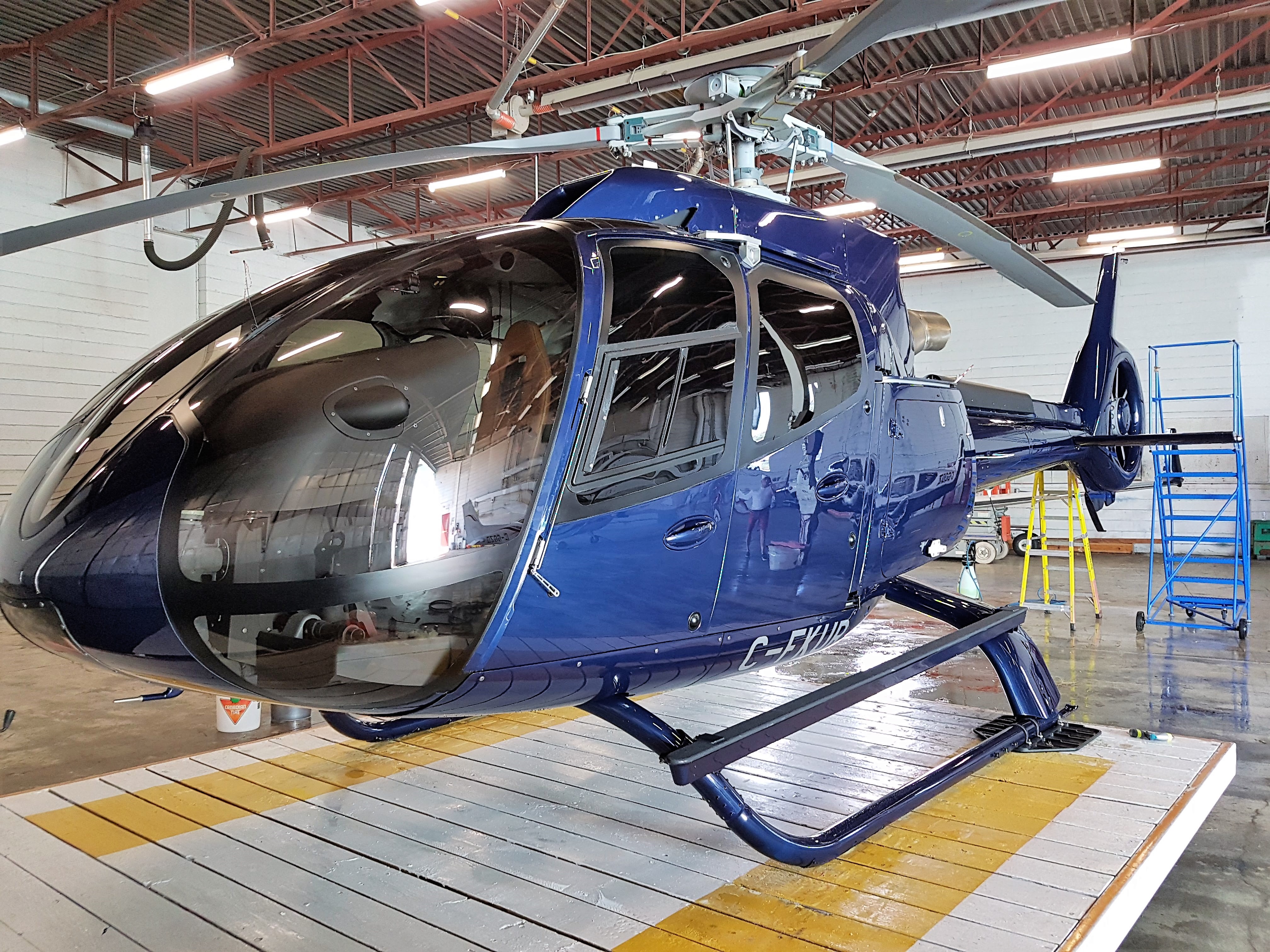
SITUATION 5
Surface exposure to operational friction
Surface contamination particularly from soot and bugs is inevitable, even on a new machine! Likewise swirls and scratches will develop rapidly on any paintwork and transparencies.
The solution: AFNTM Extreme Resilience
Put an immediate and permanent stop to degradation. Our Nanotechnology will ensure all surfaces are isolated from UVs and regular contaminants such as turbine soot, bugs, acid rain and regular wear and tear....
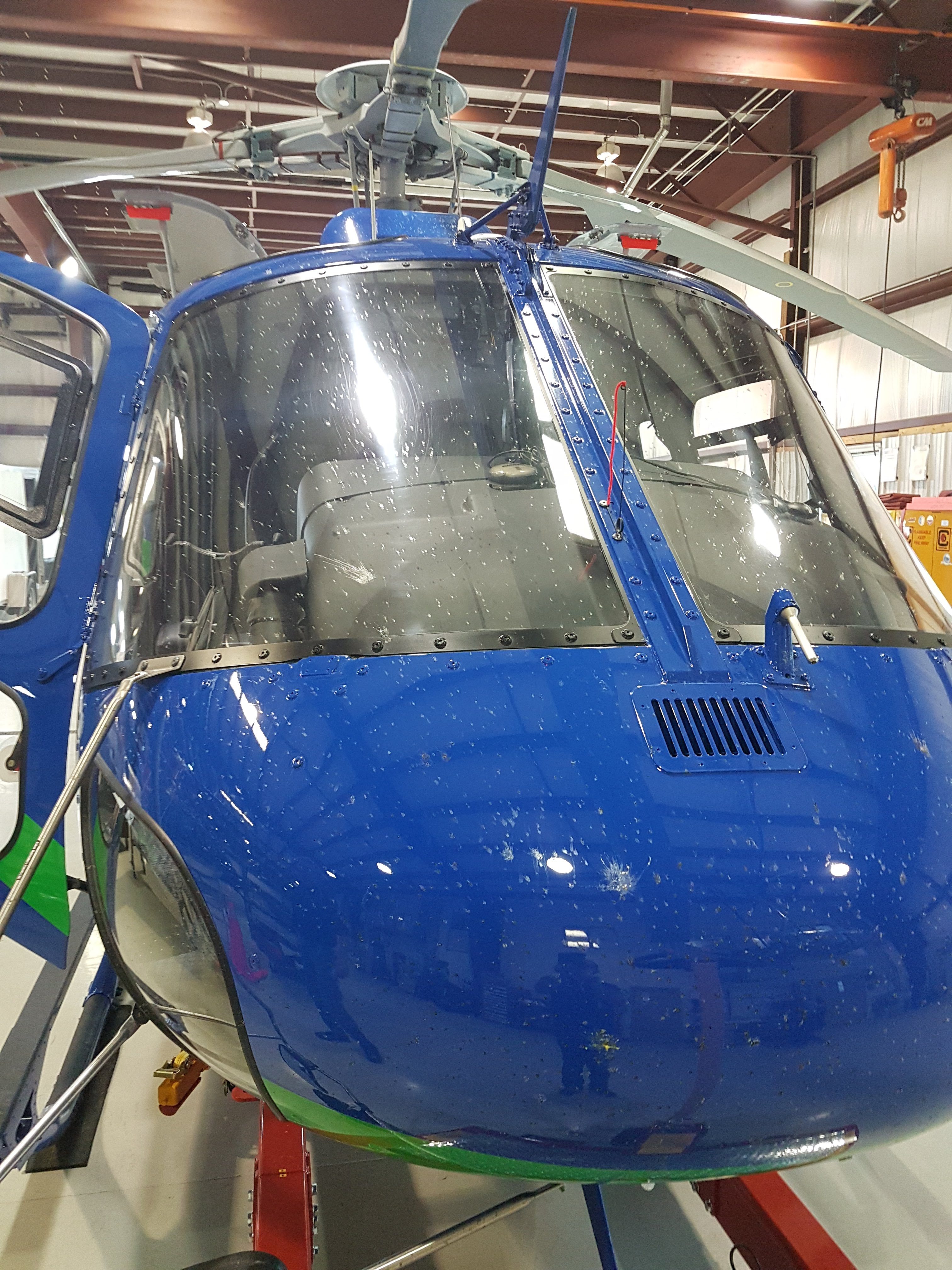
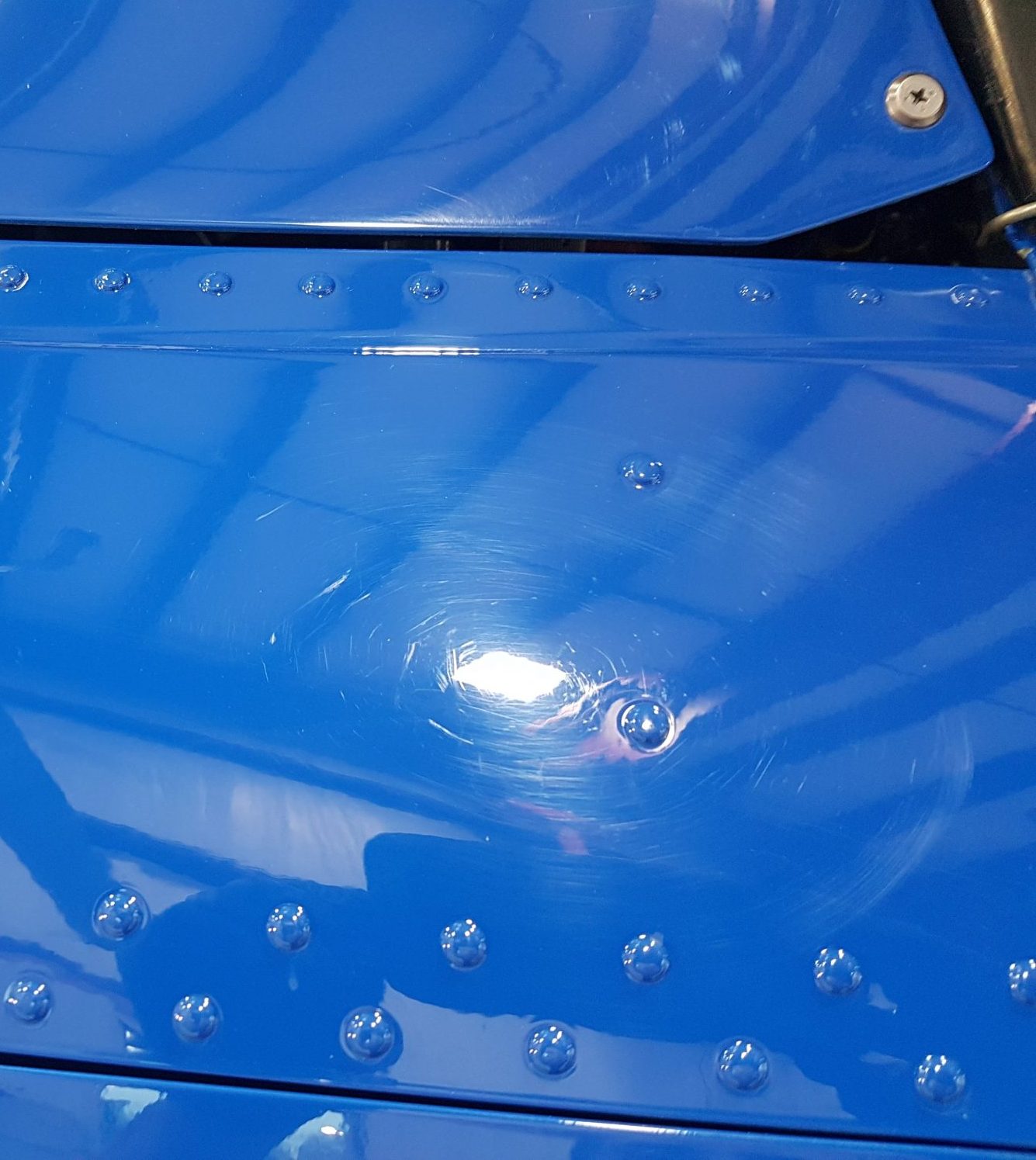
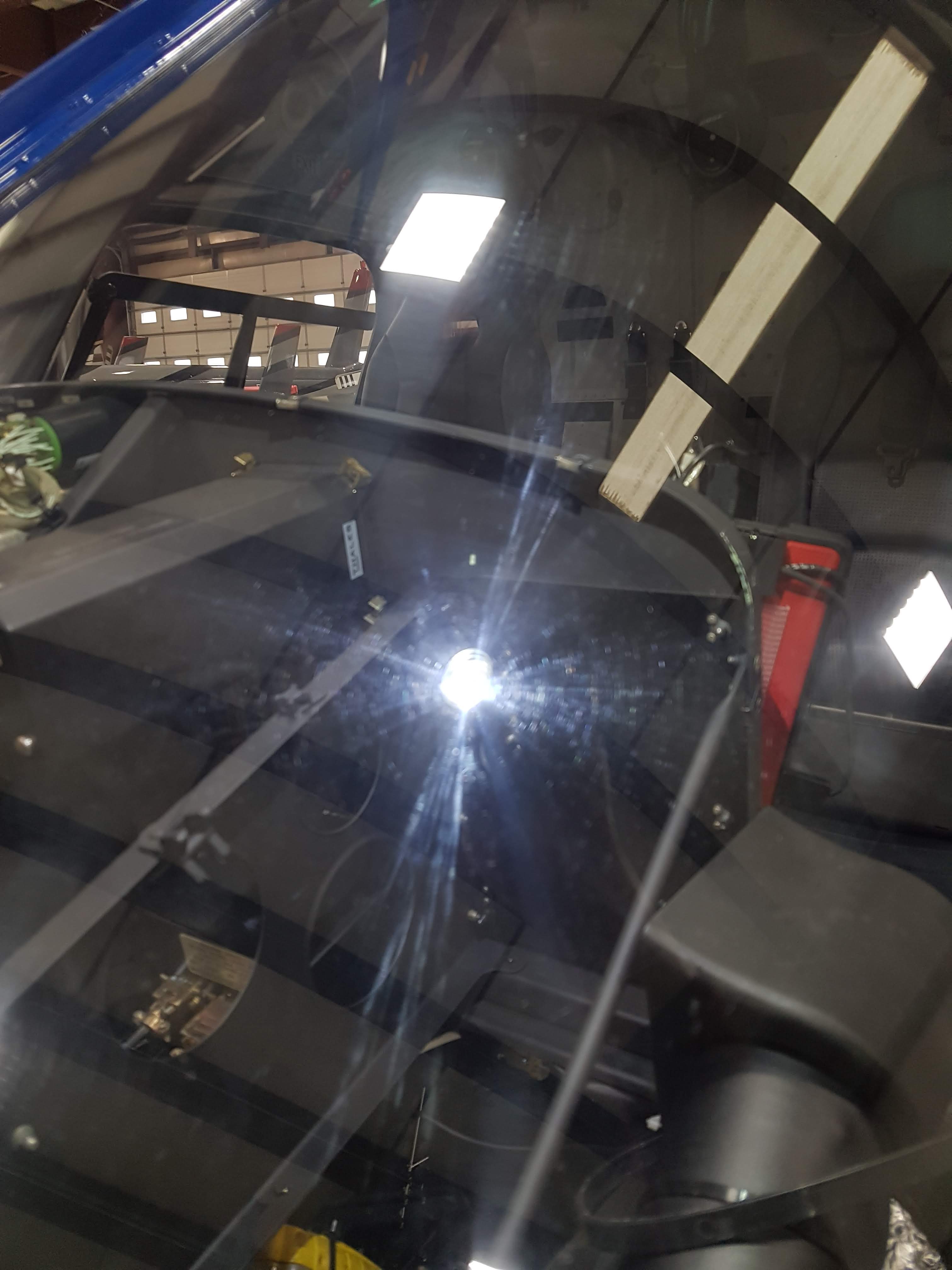
2017 Airbus H125
Less than 1 year after delivery: inevitable windshield swirls, bug impacts, paint scratches...
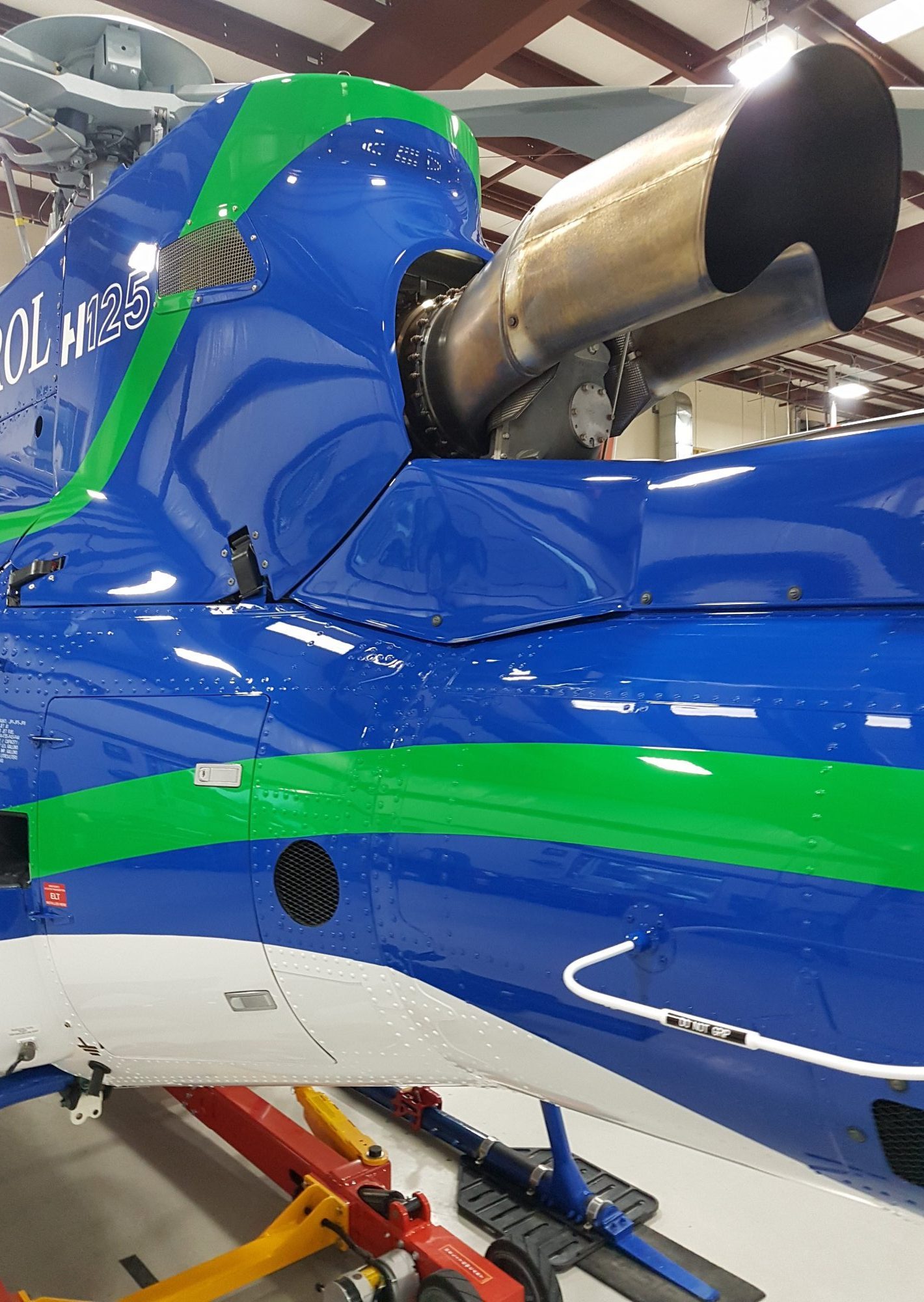
Elevated Surface Finish Permanently

AFNTM Bug Shielding
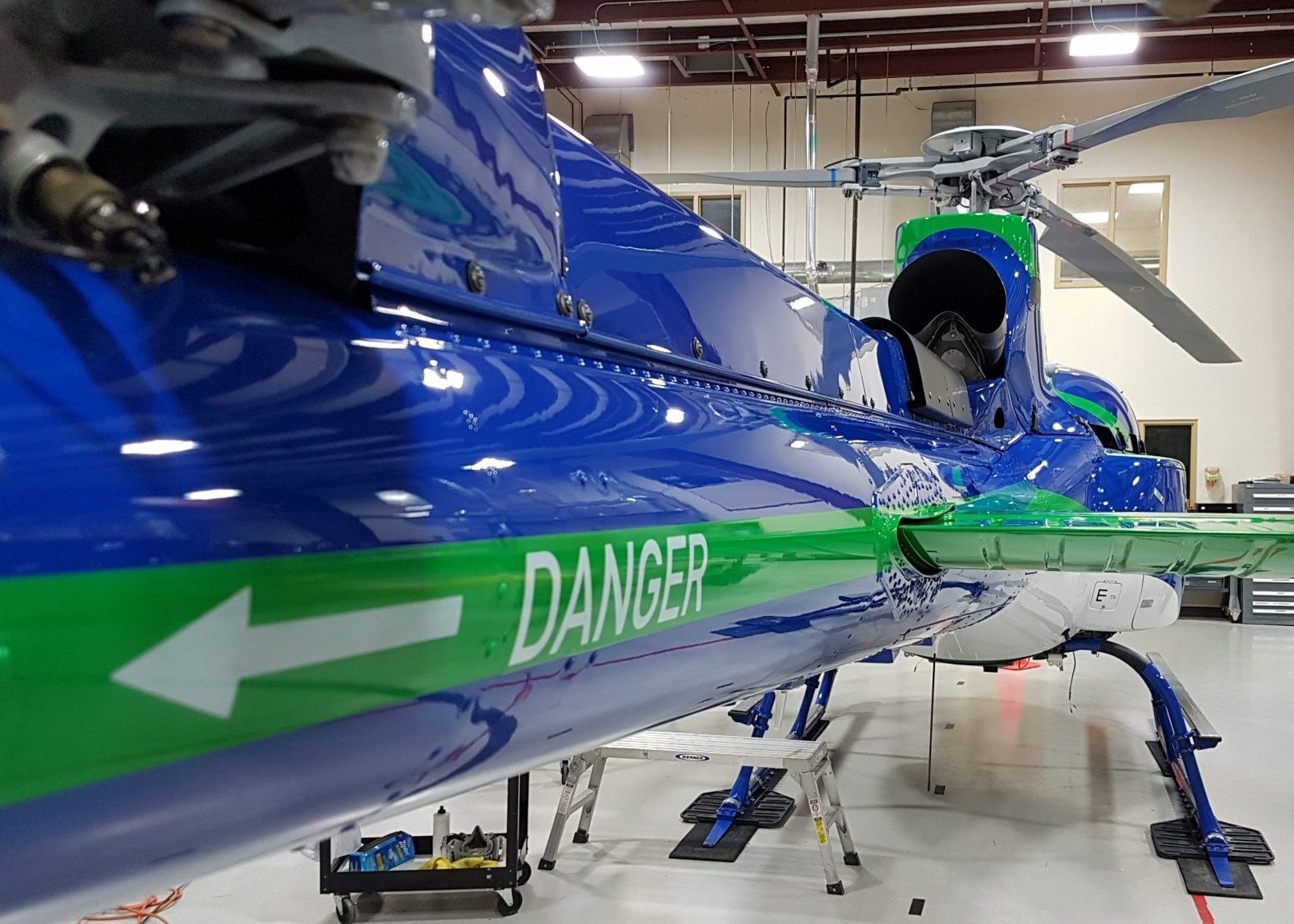
Nanotech sleekness to minimize soot adhesion & accelerate clean ups
